Cos'è un frantoio?
Prima di scoprire tutti i diversi tipi di frantoio, dobbiamo sapere cos'è un frantoio e a cosa serve. Un frantoio è una macchina che riduce le rocce di grandi dimensioni in rocce più piccole, ghiaia o polvere di roccia. I frantoi vengono utilizzati principalmente nell'industria mineraria e nell'edilizia, dove vengono utilizzati per frantumare rocce e massi molto grandi in pezzi più piccoli. I frantoi sono comunemente utilizzati anche per lavori come la frantumazione dell'asfalto per lavori stradali o progetti di demolizione. I frantoi sono disponibili in un'ampia varietà di dimensioni e capacità, dai piccoli frantoi a mascelle che costano quanto un camion nuovo ai frantoi a cono extra grandi che costano milioni di dollari. Con tutta questa scelta vorrai assicurarti che quello che sceglierai abbia la potenza e le capacità necessarie per il tuo progetto specifico. Nella maggior parte dei casi, avere un frantoio a tua disposizione può farti risparmiare una notevole quantità di tempo e manodopera poiché non dovrai fare tu stesso la frantumazione manuale dei materiali. Ciò li rende una risorsa inestimabile per chiunque abbia bisogno di frantumare materiali in modo rapido ed efficiente.
Breve storia dei frantoi
Il primo brevetto statunitense per una macchina per la frantumazione delle rocce risale al 1830. La sua tecnologia chiave era il concetto del martello a caduta, trovato nel noto mulino per francobolli, che sarebbe stato ripetutamente collegato all'età d'oro dell'estrazione mineraria. Dieci anni dopo, venne rilasciato un altro brevetto statunitense per un frantoio a urto. Il primitivo frantoio ad urto era costituito da una scatola di legno, un tamburo cilindrico di legno, su cui erano fissati dei martelli di ferro. Sebbene entrambi i brevetti siano stati concessi, nessuno dei due creatori ha mai commercializzato le proprie invenzioni.
Eli Whitney Blake inventò, brevettò e vendette il primo vero frantoio per rocce nel 1858, noto come Blake Jaw Crusher. Il frantoio di Blake fu così influente che i modelli odierni sono ancora paragonati ai suoi progetti originali. Questo perché il Blake Jaw Crusher ha integrato un principio meccanico chiave – il collegamento a ginocchiera – un concetto con cui gli studenti di meccanica hanno familiarità.
Nel 1881, Philetus W. Gates ricevette un brevetto statunitense per il suo dispositivo che presentava le idee di base dei frantoi rotanti di oggi. Nel 1883 Blake sfidò Gates a frantumare 9 metri cubi di pietra in una gara per vedere quale frantoio avrebbe finito il lavoro più velocemente. Il frantoio Gates ha completato l'operazione 40 minuti prima!
I frantoi rotanti di Gates furono preferiti dall'industria mineraria per quasi due decenni fino all'inizio del secolo, intorno al 1910, quando i frantoi a mascelle di Blake videro una rinascita di popolarità. La domanda di frantoi a mascelle a bocca larga salì alle stelle quando l'industria iniziò a comprenderne il potenziale come frantoi primari nelle cave di roccia. Attraverso la ricerca e lo sviluppo di Thomas A. Edison, macchine giganti furono innovate e collocate negli Stati Uniti. Sono stati sviluppati anche frantoi a mascelle di piccole dimensioni come frantoi secondari e terziari.
Gli studi di Edison nel campo dell'estrazione e della frantumazione hanno lasciato un'eredità che ha migliorato per sempre il modo in cui vengono ridotte le rocce e i materiali di grandi dimensioni.
La frantumazione è il processo di riduzione o scomposizione del materiale di dimensioni maggiori in materiale di dimensioni più piccole. Esistono quattro modi fondamentali per schiacciare.
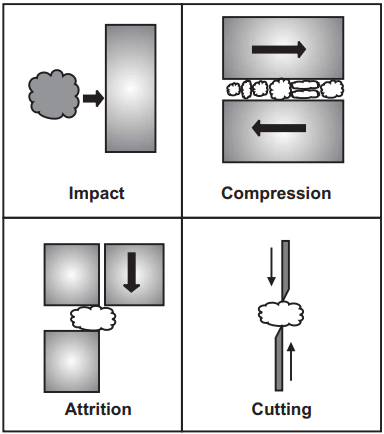
Impatto: collisioni istantanee di oggetti di grandi dimensioni uno contro l'altro con materiale interposto. Entrambi gli oggetti possono essere in movimento oppure uno può restare fermo mentre l'altro lo urta. Esistono due tipi principali di riduzione dell’impatto, gravità e dinamica.
Attrito: sfregamento del materiale tra due superfici solide. Questo è un metodo appropriato quando si riducono materiali meno abrasivi perché consuma meno energia durante il processo. I materiali robusti non sarebbero altrettanto efficienti.
Taglio: tipicamente combinato con altri metodi di riduzione, il taglio utilizza un metodo di rifilatura e viene utilizzato quando si desidera un risultato grossolano. Questo metodo di riduzione è spesso utilizzato nella frantumazione primaria.
Compressione: un elemento meccanico chiave dei frantoi a mascelle, la compressione riduce i materiali tra due superfici. Ottimo per materiali molto duri e abrasivi che non si adattano ai frantoi ad attrito. La compressione non è adatta per qualsiasi cosa appiccicosa o gommosa.
La scelta del tipo corretto di metodo di frantumazione dipende sia dal tipo di materiale che si sta frantumando che dal prodotto desiderato. Successivamente, devi decidere quale tipo di frantoio è più adatto al lavoro. Tenere presente l’utilizzo e l’efficienza energetica è sempre una considerazione importante. L'utilizzo del tipo sbagliato di frantoio può portare a costosi ritardi e consumare più energia del previsto durante il processo.
Quali sono i diversi tipi di frantoi?
Esistono molti tipi diversi di frantoi, dai frantoi a mascelle ai frantoi a impatto e ai frantoi a cono. La frantumazione è un processo versatile e il tipo di frantoio necessario dipende dalla "fase" della frantumazione. Le tre fasi principali della frantumazione sono primaria, secondaria e terziaria, ognuna con i propri vantaggi unici. La frantumazione primaria prevede l'utilizzo di un oggetto di grandi dimensioni come forza iniziale per frantumare rocce e massi molto grandi e duri in pezzi più piccoli prima che passino alla fase secondaria. La frantumazione secondaria scompone ulteriormente i materiali prima che raggiungano il livello terziario, creando un prodotto ancora più fine che può poi essere utilizzato in vari progetti industriali. Ogni tipo di frantoio per ogni specifica fase di frantumazione è spiegato più dettagliatamente di seguito.
Attrezzatura primaria di frantumazione
Come suggerisce il nome, questo tipo di frantumazione è il primo del processo. I materiali Run of Mine (ROM) vengono portati direttamente dai progetti di esplosione e frantumati in un frantoio primario per il primo ciclo di frantumazione. A questo punto il materiale riceve la prima riduzione dimensionale rispetto allo stato grezzo. La frantumazione primaria produce materiali che vanno dada 50" a 20"in media. I due tipi principali di frantoi primari sono:
Frantoi a mascelle
Grandi quantità di materiale vengono immesse nella ganascia a "V" di questo frantoio e vengono ridotte utilizzando la forza di compressione. Un lato della V rimane fermo mentre l'altro lato della V oscilla contro di essa. Il materiale viene spinto dall'ampia apertura della V al punto più stretto della V creando un movimento di frantumazione. I frantoi a mascelle sono macchinari pesanti e di grandi dimensioni, generalmente costruiti in ghisa e/o acciaio. Spesso considerati una macchina di base, i frantoi a mascelle hanno il loro posto nel settore. Sono spesso utilizzati per ridurre la roccia in ghiaia non uniforme.
Frantoi rotanti
Il materiale di miniera viene trasferito nella tramoggia di livello superiore di un frantoio rotante. Le pareti della tramoggia del frantoio rotante sono rivestite con pezzi a “V”, il mantello e il controbattitore, come un frantoio a mascelle ma a forma di cono. Il minerale viene scaricato attraverso il foro di uscita inferiore più piccolo del cono. Mentre il cono non si muove, un movimento di frantumazione interno viene creato da un albero rotante su un'asta verticale. Viene creata un'azione continua che lo rende più veloce del frantoio a mascelle con un minore consumo di energia. Spesso più piccoli e più costosi di un frantoio a mascelle, i frantoi rotanti sono adatti per quantità maggiori di materiali quando si desidera una forma più uniforme
Attrezzatura secondaria di frantumazione
Dopo che i materiali hanno superato il primo ciclo di frantumazione, vengono immessi in un frantoio secondario per essere ulteriormente sminuzzati. La dimensione media in ingresso per un frantoio secondario varia dada 13" a 4"durante questa fase. La frantumazione secondaria è particolarmente importante per produrre materiale selezionato che verrà utilizzato in progetti governativi. Ad esempio materiale frantumato per il fondo stradale e il riempimento. Di seguito vengono discusse le principali tipologie di macchine di frantumazione per la lavorazione secondaria.
Frantoi a cono
I frantoi a cono sono una delle scelte principali per la frantumazione secondaria. Un frantoio a cono è una macchina potente che viene utilizzata nelle industrie su larga scala per frantumare vari tipi di materiali in dimensioni più piccole. Funziona applicando pressione sul materiale e comprimendolo contro un mantello rotante per creare compressione e forza. Il materiale frantumato viene prima scomposto nella parte superiore del cono dove poi cade nella parte inferiore del cono, più stretta. A questo punto il frantoio a cono frantuma nuovamente il materiale in una pezzatura ancora più piccola. Questo continua finché il materiale non è abbastanza piccolo da cadere dall'apertura inferiore. Il materiale proveniente da un frantoio a cono può essere utilizzato per molti progetti diversi, tra cui la base stradale nei progetti di costruzione, il rifacimento della pavimentazione in asfalto o nelle cave di ghiaia per la costruzione di strade. I frantoi a cono sono adatti per materiali medio-duri e duri, come la roccia vergine proveniente dalle cave.
Frantoi a rulli
Un frantoio a rulli riduce il materiale comprimendolo tra due cilindri rotanti, paralleli tra loro. I cilindri sono montati orizzontalmente, uno appoggiato su robuste molle e l'altro incorniciato in modo permanente. Il materiale viene quindi alimentato tra i due. La modifica della distanza tra i rulli consente di controllare la dimensione desiderata del materiale in uscita. Ogni cilindro è facilmente regolabile e rivestito con manganese per la massima usura a lungo termine. I frantoi a rulli in genere forniscono materiale fine e non sono adatti per materiali duri o abrasivi.
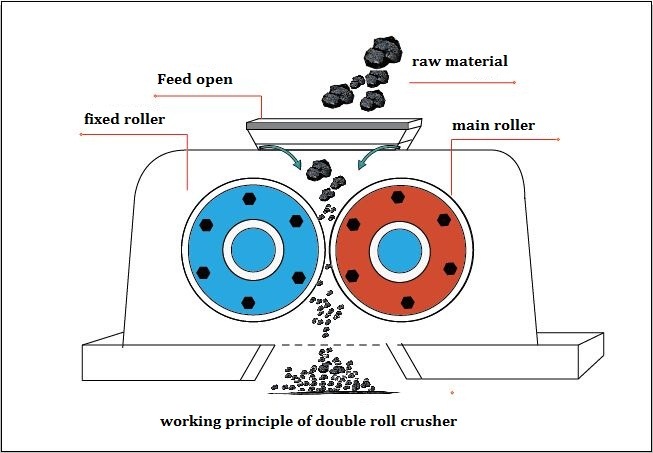
Mulini a martelli e frantoi a urto
Uno dei frantoi più versatili disponibili, i mulini a martelli e gli impattatori possono essere frantoi primari, secondari e terziari. I frantoi con mulino a martelli utilizzano continui colpi di martello per frantumare e disintegrare il materiale. Sono tipicamente rotanti orizzontalmente in un involucro del cilindro chiuso. I martelli sono fissati ad un disco e oscillano con la forza centrifuga contro l'involucro. Il materiale viene immesso nella parte superiore e frantumato cade attraverso il foro nella parte inferiore. Troverai mulini a martelli utilizzati in settori come l'agricoltura, la medicina, l'energia e altro ancora. Forniscono alcuni degli output più efficienti disponibili, sono portatili e possono gestire quasi tutti i materiali.
I frantoi a urto hanno un principio di funzionamento molto simile, tranne per il fatto che invece di colpire il materiale come un martello, le parti rotanti lanciano invece il materiale contro una piastra d'urto che lo frantuma. Sono disponibili anche in configurazioni ad albero orizzontale o verticale a seconda della potenza desiderata.
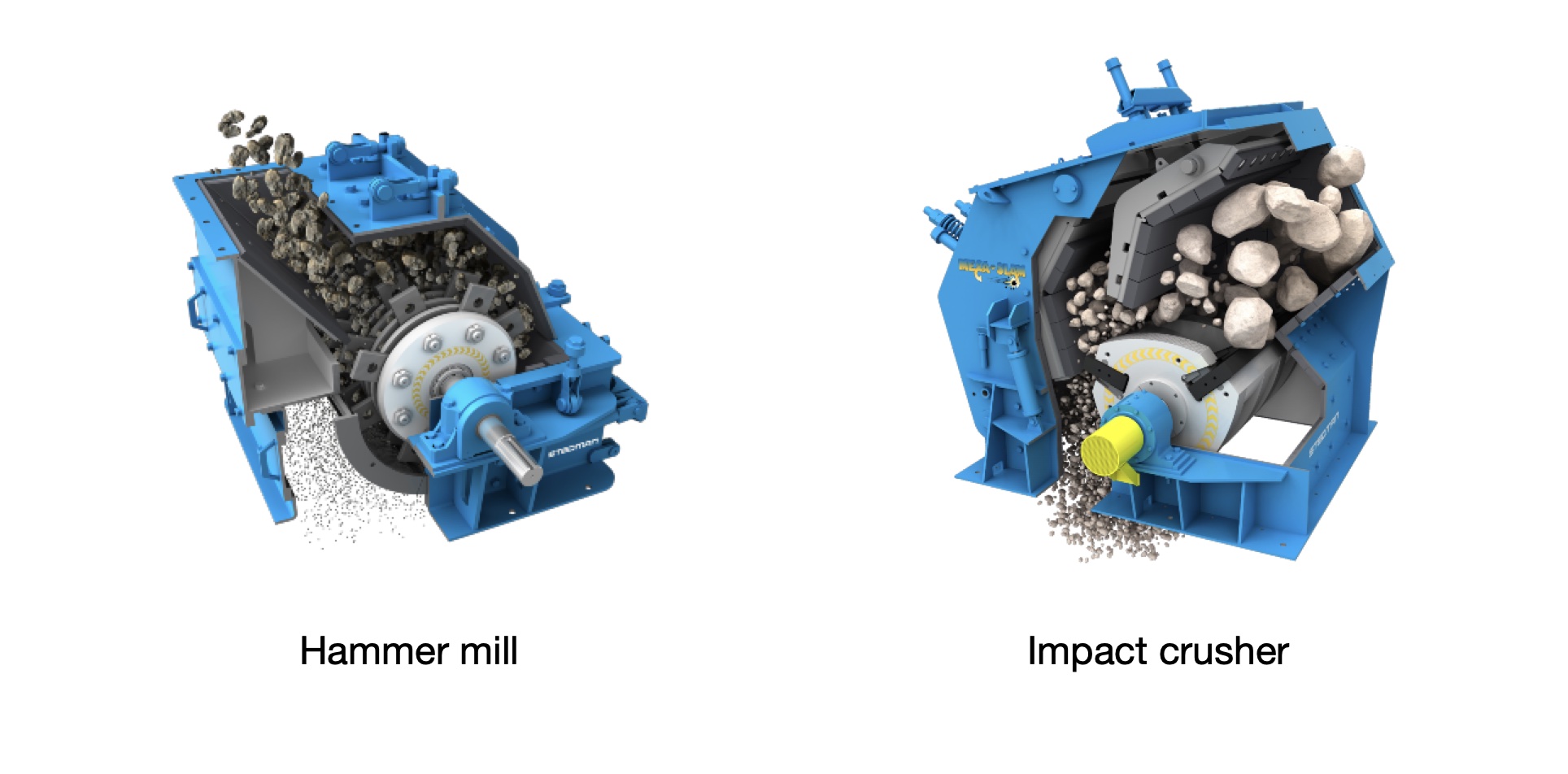
Orario di pubblicazione: 02 febbraio 2024